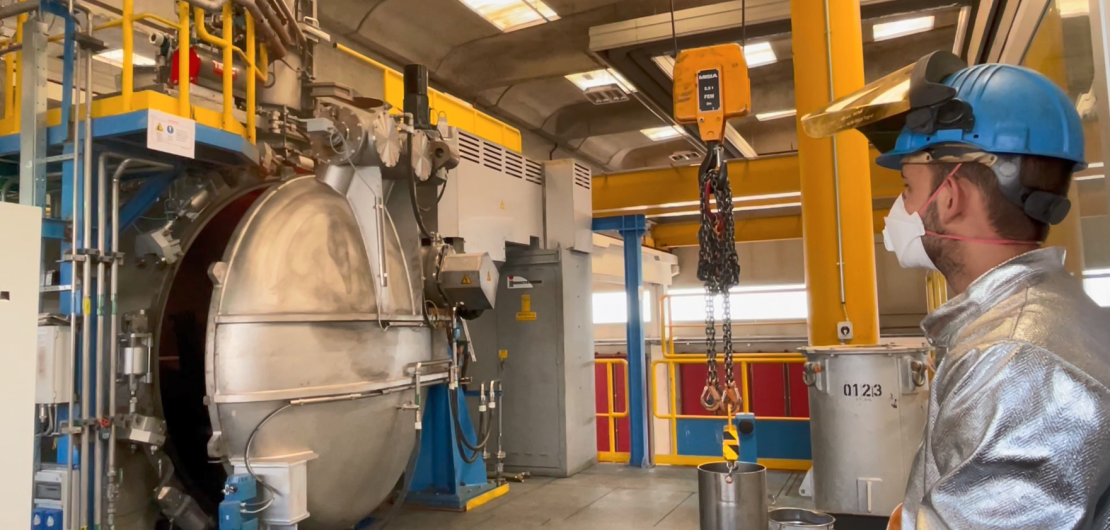
How metal 3D printing can bring change to the world’s most resource-intensive industries
– The Politecnico di Milano is leading an international consortium dedicated to improving resource efficiency in the construction and automotive sectors through metal 3D printing.
– It is hoped that additive manufacturing technology will help usher in a new era of increased customisation and optimisation and allow companies to reduce waste and energy consumption during the steel manufacturing process.
According to the European Commission, 30% of all waste produced annually in the EU comes from the construction and demolition industry.
That’s why one international research project, coordinated by the Politecnico di Milano, is focused on reducing the sector’s carbon footprint, along with that of the automotive industry, through innovative steel 3D printing technology.
ConstructAdd, financed by the European Research Fund for Coal and Steel, is bringing together companies, technology, and research centres from five European countries to improve resource efficiency in the steel manufacturing industry.
“The main objective of ConstructAdd is to bring metal 3D printing technology into the mainstream of the construction and automotive industries,” explains project coordinator Dr. Alper Kanyilmaz. “Why? Because the current objectives of governments worldwide, and society as a whole, are reducing carbon emissions and dealing with waste problems.”
“These concerns, which are major challenges for the construction industry in particular, cannot easily be solved with conventional techniques, simply because conventional techniques were invented for problems of the past.”
Specifically, ConstructAdd aims to prove that the introduction of metal 3D printing can create less waste during fabrication while reducing energy consumption by approximately 30%.
Along with the Politecnico di Milano, project partners in ConstructAdd include IMDEA Materials Institute in Madrid, the University of Pisa, RWTH Aachen, Prima Industrie S.p.A., BLM Group, Det Norske Veritas, CIMOLAI SPA, VALLOUREC, MIMETE, and ArcelorMittal Vitry.
“Given around one-third of all the waste produced around the world each year comes from the construction industry, steel production has a major role to play here,” says Dr. Kanyilmaz. “The current manufacturing techniques available are not easily optimised, and there is a lot of material wasted.
“For example, during the cutting and welding of steel plates. Also, using conventional construction techniques, a lot of material is used where it isn’t needed and placed in unnecessary spots.”
This is where metal 3D printing, or metal additive manufacturing as it is also known, comes in.
Printing customised components and joints from scratch eliminates the production of scrap metal in the process that would otherwise result as a byproduct of crafting parts from an existing steel plate.
It will also allow for the optimisation of the manufacturing process and greater flexibility on the part of construction companies, who will be able to print certain components on-site rather than relying on transportation.
Steel 3D printing holds particular appeal, given its essential nature to the construction industry, thanks to its high strength-to-weight ratio, tensile strength, flexibility, and versatility, among other factors.
The EU is currently the world’s second-largest steel producer after China, manufacturing more than 170 million tons of the metal annually.
“When we talk about additive manufacturing, there are already some very interesting outcomes in other industries. For example, some small houses are being built via this method with concrete,” says Dr. Kanyilmaz.
“Steel comes into play in printing critical components that can be integrated into larger structures. Steel is far more resistant and ductile compared to other materials. So, it offers more opportunities to manufacture more complex geometries which can withstand higher stress and fatigue loads.”
“In any future where 3D printing becomes mainstream in the construction industry, steel will maintain those advantages. That is what makes developing additive manufacturing technology in this area so attractive.”